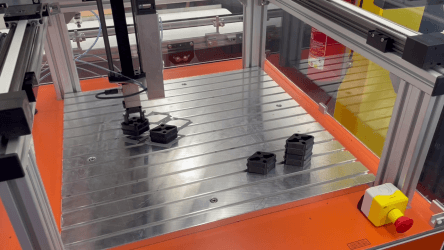
Compliance with the customer-specific cycle time with a room gantry robot
Hardware Price:
Max Speed
0.5
m⁄s
Repeatability
0.5
mm
DOF
3
igus Gantry Robot with Schunk EGP Gripper: Precise Pick-and-Place Solution
Automating pick-and-place tasks is crucial for improving production efficiency. In this customer test, the igus gantry robot, equipped with the Schunk EGP gripper, demonstrates its capabilities in handling plastic components. The system moves objects from one position to another with precise and efficient motions, meeting strict cycle time requirements for the project. This setup showcases how automation can streamline workflows while ensuring reliability and productivity.
What is the Application?
The system automates pick-and-place operations for plastic components, accurately transferring items within defined spaces to optimize production processes.
What are the Advantages of the Solution?
Cycle Time Optimization: Rapid and reliable movements meet demanding project timelines.
Improved Accuracy: Reduces errors in handling objects due to precise robotic control.
Enhanced Workflow Efficiency: Frees up human labor for more value-added tasks.
What are the Advantages of the Robot?
The igus gantry robot combined with the Schunk EGP gripper delivers robust automation:
Precision Handling: The EGP gripper ensures firm and reliable gripping of components.
Compact and Modular Design: Easy integration into various production environments.
High Reliability: Consistent movements improve overall system performance.
Revolutionizing Pick-and-Place Tasks with Automation
This igus gantry robot setup showcases a precise and efficient solution for handling plastic components. By meeting customer-specific cycle time requirements, this automation system exemplifies how robotics can enhance accuracy, productivity, and scalability in modern manufacturing workflows.
2 Components